Ключевые слова: дорожные покрытия, бетонный керн, шелушения, трещина, абсорбция, нанесение состава, обработка дорожного покрытия, морозостойкость, водонепроницаемость.
Общепризнанными преимуществами бетонных покрытий являются стабильные транспортно-эксплуатационные показатели и высокая долговечность. Однако, дефекты и деформации, наблюдаемые на цементобетонных покрытиях, требующие постоянного внимания и значительных ремонтных затрат, уже сейчас свидетельствуют о том, что срок службы бетонных покрытий будет ниже, чем за рубежом. Причинами этого могут быть ошибки при проектировании, строительстве, ремонте и, что немаловажно, невысокое качество эксплуатационного содержания этого типа покрытий.
Вместе с тем, в зарубежной практике широкое применение находят технологии для повышения устойчивости поверхностного слоя бетона к эксплуатационным и природно-климатическим воздействиям, в частности, обработка пропиточными укрепляющими составами на начальной стадии появления мелкого шелушения и морозных волосяных усадочных трещин.
Шелушение поверхности на начальной стадии может быть очаговым (в отдельных местах) или сплошным (по всей плите или значительной её части), неглубоким (глубиной несколько мм), когда отшелушивается под действием циклического замораживания и оттаивания, солей-антиобледенителей и транспортных средств только цементное «молочко» (рис.1).
Рис. 1. Шелушение на начальной стадии по всей плите
Поверхностные, относительно неглубокие (несквозные) морозные волосяные усадочные трещины, хаотически расположенные (рис. 2), чаще всего, вызываются нарушением в составе бетона и технологии работ, применением несоответствующих стандартам материалов. Они образуются в местах постоянного замачивания.
Данные виды дефектов опасны тем, что, проникая влага и противогололедные реагенты в поры бетона начинают ее разрушать.
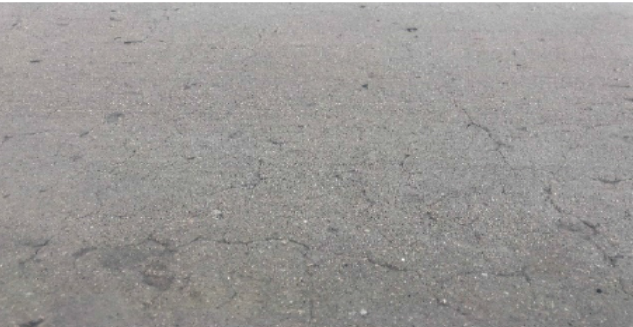
Рис. 2. Мелкие волосяные усадочные трещины
Однако, шелушение поверхности покрытия может свидетельствовать о недостаточной морозостойкости только поверхностного слоя, а не всего бетона в плите.
Также, одним из основных причин появления шелушения и волосяных усадочных трещин на начальной стадии это обильное использование противогололедных реагентов (солей) в первую зиму эксплуатации покрытия.
Защитить верхний слой покрытия от этих дефектов может его системная пропитка укрепляющими составами на основе кристаллизации. Стабилизацию поверхности бетона целесообразно проводить при начальной стадии образования шелушения (разрушение цементного камня на глубину до 5 мм).
Проникая в поверхностный слой бетона, они образуют в порах и капиллярах кристаллические труднорастворимые в воде соединения, что способствует упрочнению структуры цементобетона, повышению морозостойкости и износоустойчивость покрытия.
Рис. 3. Гигроскопическое и гидрофильное поведение кристаллов пропиточного состава
Сначала состав вступает в реакцию с воздухом с образованием гидрофобизатора и одновременно проникает в бетон, образуя кристаллы в порах и пустотах бетона. Эти кристаллы растут, перемещаются в направлении источника воды, эффективно герметизируя структуру бетона (рис. 3).
Применение данных пропиточных составов:
− предотвращает проникновения воды с поверхности;
− уменьшает диффузию ионов хлоридов;
− уменьшает шелушение поверхности;
− защищает цементобетон от выкрашивания вследствие замораживания — оттаивания;
− герметизирует волосяные трещины.
При использовании пропитки бетона необходимо учитывать, что поверхность покрытия должна быть очищена от загрязняющих примесей (желательно тщательно промыта), а также — от плёнкообразующего материала, применяемого для ухода за свежеуложенным бетоном и остающимся в его порах после открытия движения.
Подготовку поверхности покрытия следует производить следующим образом: сначала поверхность очистить от пыли и мусора щетками машины комбинированной дорожной машиной (КДМ), а затем промыть поливомоечной машиной.
Обработку дорожного покрытия рабочим составом необходимо выполнять после полного высыхания воды с поверхности дорожного покрытия.
Нанесение состава на бетонные покрытия осуществляется любыми машинами, которые могут точно и равномерно распределять его с заранее установленной нормой расхода. При небольших объемах работ состав можно распределять вручную (к примеру, краскопультом). На больших участках можно использовать поливомоечные машины или чистые гудронаторы. Норма дозирования зависит от рекомендаций производителей и варьируется в пределах 0,2- 0,3 л/м2.
Рис. 4. Нанесение состава водовозом с распределительной рампой
Рис. 5. Нанесение состава ручным способом
Выполняют работы при температуре наружного воздуха не ниже +10°С, при этом в течение 48 ч поверхность бетона необходимо предохранять от увлажнения.
Движение на обработанном участке следует открывать не ранее, чем через 3–4 ч (пример разработанного пропиточного состава на фотографиях). В течение первых суток после розлива состава, желательно, скорость движения необходимо ограничить до 40 км/ч.
Рис. 6. Покрытие сразу после обработки
В процессе производства работ по нанесению состава на покрытие следует контролировать: расход состава; качество обработанного покрытия.
Нанесение состава должно проводиться равномерно по всей поверхности. Проверку расхода состава определяют визуально по сплошности розлива, по расходу на 1 м 2 поверхности и по скорости впитывания раствора.
Контроль качества защитного слоя обработанного цементобетона проводят спустя 2–3 сут после обработки, опрыскивая поверхность водой. Если вода не впитывается, а бетон не увлажняется (не темнеет), гидрофобную обработку следует считать удовлетворительной.
Глубина пропитки цементобетонного дорожного покрытия определяется на взятых кернах. Для этого на продольный разрез керна наносят капли воды и по впитыванию их в бетон определяют глубину пропитки (она должна быть не менее 2 мм).
Контроль эффективности защиты осуществляют при помощи 10 % раствора соляной кислоты, наносимой на покрытие, подвергнутое пропитке.
Рис. 7. Вода не проникает на обработанном участке
Отсутствие взаимодействия кислоты с цементным камнем (последнее на необработанном бетоне проявляется в виде вспенивания раствора) говорит о высоком качестве полученной защиты.
И, главным показателем эффективности пропиточного состава является показатели водонепроницаемости, морозостойкости и стойкость к противогололедным реагентам от выбуренных кернов, согласно ГОСТ. Вся методика испытаний описана.
Рис. 8. Определение морозостойкости обработанных и необработанных образцов бетона
На вновь построенных покрытиях пропитка может быть проведена не ранее, чем через 6 месяцев после укладки бетона или после промывки покрытия под давлением для вымывания пленкообразующих материалов.
Существующие покрытия, уже подвергавшиеся воздействию антигололедных химреагентов, следует обрабатывать в летом или осенью, чтобы было достаточно времени для вымывания выпадающими осадками остатков, примененных ранее химреагентов.
При наличии на поверхности бетона следов резины от шин, маркировочных красок или каких-либо других загрязнений на участках покрытий, которые могут препятствовать и ухудшать проникновение пропитывающих составов в поры бетона, обработка покрытий не допускается до полной их чистки от покрытия.
Особенность работ по стабилизации поверхности бетона состоит в том, что помимо разрушенных участков, необходимо так же выполнить работы на соседних участках плит. Для определения границ и размеров разрушенных участков проводят диагностику состояния этих плит.
Литература:
- Адилходжаев А. И., Амиров Т. Ж. Некоторые способы повышения долговечности дорожных бетонных и железобетонных изделий автомобильных дорог // Вестник ТАДИ. Научно-технический журнал. –Ташкент. -2018. -№ 1. с.38–43.
- Саатова Н. З. Остаточный ресурс железобетонных пролетных строений автодорожных мостов, подверженных солевой коррозии. автореферат дис. канд. техн. наук: — Ташкент, 2017. — 25 с.
- Джалилов А.Т., А. М. Карабаев, Т. Ж. Амиров и др. Способ защиты бетонных и железобетонных изделий // IAP — 05604. — Ташкент. Патентный бюллетень Узбекистана. — 29.06.2018. -№ 6.