Статья посвящена рассмотрению профессий и компетенций будущего на основе новой индустриальной модели. Проанализированы характерные особенности аддитивных технологий. Обобщен и представлен опыт реализации ФГОС СПО по специальности «Аддитивные технологии».
Ключевые слова: аддитивные технологии, пластиковая нить для 3D, притинг, экструдер.
В настоящее время на предприятиях и в учреждениях нашли широкое применение аддитивные технологии. Аддитивные технологии — инновации в сфере промышленности и производства. Цифровые новшества с использование 3D принтинга.
Аддитивные технологии — изготовление (построение) физического объекта (детали) методом послойного нанесения (добавления, англ.- «add») материала, в отличие от традиционных методов формирования детали, за счет удаления (sudtraction — вычитание) материала из массива заготовки. Суть аддитивных технологий можно проиллюстрировать простым примером на рисунке 2.
Преимущества аддитивных технологий
Аддитивные технологии, успешно используемые в машиностроении и других сферах, дают очевидные выгоды:
Экономия ресурсов. Готовые изделия «выращивают», благодаря чему можно говорить о безотходном производстве. Кроме того, исключаются расходы на утилизацию отходов. Для сравнения, потери материала на заготовках при использовании консервативных методов металлообработки могут доходить до 85 %;
Рис.1. Аддитивные технологии
Ускорение процесса производства . Сокращение цикла от момента разработки проекта до выпуска готовых изделий дает конкурентные преимущества. Компьютерное моделирование не требует долгих расчетов и многочисленных чертежей. При этом скорость не вредит качеству;
Точность параметров . При послойном синтезе удается достигать максимального соответствия по плотности, остаточному напряжению, техническим показателям. Прочность изделий на 20–30 % выше, чем у литых и кованых.
Мобильность . Запуск производства новой серии изделий не требует длительной подготовки, закупки громоздкого оборудования. Процесс гибкий, что позволяет адаптироваться к меняющемся условиям рынка. Модели можно передавать по средствам компьютерной техники в любой уголок планеты в считаные секунды.
Для таких отраслей как авиастроение, важное преимущество- снижение веса изделий, получаемых за счет внедрения аддитивных технологий. Отдельные детали удается сделать легче на 40–50 % без потерь в прочности.
На рисунке 2 представлена сравнительная таблица преимуществ аддитивных технологий с традиционными методами формирования детали, за счет удаления материала из массива заготовки.
Рис.2. Сравнительная таблица преимуществ традиционного производства и аддитивных технологий
FDM (Fused Deposition Modeling) — моделирование методом наплавления (метод моделирования путем послойной укладки расплавленной нити Преимущества: высокая точность исполнения прототипа; высокая скорость 3D-печати; возможность использования широкого спектра полимеров; низкая стоимость 3D-печати прототипа. Недостатки: ограничения по допускам размерности 3D-печати; необходимость в постобработке.
Материалы для печати: термопластичная нить (PLA, ABS, PET, TPU) Точность измерения: ±0.5 % (нижний предел ±0.5 mm).
Общее применение: электрические корпуса; проверка форм и соответствия; монтажные и установочные приспособления; образец выплавляемых моделей.
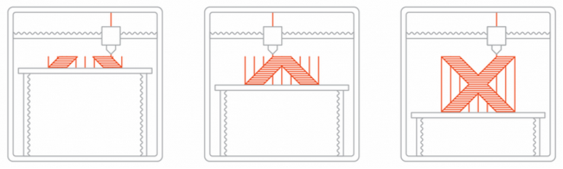
Рис.3. Моделирование методом наплавления (FDM)
Каждое образовательное учреждение, которое в своем распоряжении имеет 3D принтеры, нуждается в расходных материалах.
Порой, в организациях не хватает денежных средств, чтобы заказать расходные материалы для работы 3D принтеров (катушки пластика). В данном проекте предлагается на рассмотрение экструдер для изготовления пластиковой нити.
На данный момент существует много видов пластика для печати на 3D принтерах (FDM), стоимость их колеблется в диапазоне 800–1500 т.р за 1 катушку. При ежедневном использовании принтера, 1 катушки пластика хватает на 3 недели. В настоящий момент в нашей лаборатории 8 принтеров, исходя из этих цифр получается, что примерно за месяц мы расходуем 8 катушек на сумму 8000 т.р. Техникум заинтересован в снижении затрат на расходные материалы. Поэтому у нас возникла идея уменьшить затраты на расходный материал изготовив экструдер для изготовления пластиковой нити для 3D принтера (FDM). Что в свою очередь значительно уменьшит затраты на покупку расходных материалов.
Уменьшение затрат на расходный материал для печати на 3 D принтере, за счет самостоятельного изготовления пластиковой нити. На основании практических навыков и теоретических знаний можно изготовить экструдер для изготовления пластиковой нити для 3D принтера (FDM).
Для достижения поставленной цели необходимо было решить следующие задачи:
- Провести мониторинг имеющихся устройств для изготовления пластиковой нити и их ценового диапазона.
- Изучить типовые конфигурации устройств.
- Разработка собственного аналога устройства.
- Рассчитать себестоимость и рентабельность изготовления экструдера для изготовления пластиковой нити.
Одним из новейших устройств в мире 3D-печати является экструдер для самостоятельного изготовления пластиковой нити для 3д печати. И речь идет не печатающих головках FDM- принтеров, хотя технологии одинаковы, а речь идет о портативных настольных машинах для изготовления пластиковой нити.
Экструдер представляет собой устройство, которое путем плавления расходного материла и дальнейшего выдавливания расплавленного сырья через отверстие диаметром 1,75; 2,85 или 3мм. Фактически, экструдер представляет собой механизм мясорубки, но с дополнительным механизмом как нагревательный элемент. Именно подобные установки используются при промышленных производствах прутка для 3д печати.
Проанализировав характеристики и ценовой диапазон экструдеров для изготовления пластиковой нити для печати на 3 D принтере, мы пришли к выводу, что изготовить устройство самим будет выгодней с экономической точки зрения.
Мы спроектировали экструдер для изготовления пластиковой нити для печати на 3D (FDM). Принцип работы экструдера состоит в следующем: шаговый мотор типа Nema 23 вращает шнек, на который через бункер засыпается сырье в виде пластиковых гранул, шнек в свою очередь перемещает гранулы пластика к нагревательному элементу который расплавляет сырье до пластичного состояния, после чего попадает в головку экструдера откуда уже готовый пруток диаметром 1,75мм и выдавливается. Отсюда пластиковая нить попадает в резервуар с водой, которая имеет постоянную температуру.
Последующие движения прутка обеспечивают два электродвигателя которые наматывают его на катушку (рисунок 4).
Рис.4. Схема комплектации экструдера для изготовления пластиковой нити для печати на 3D принтере (FDM)
Исходя из этого общая стоимость нашего экструдера выходит 8500 рублей, что намного дешевле зарубежных аналогов. За сет этого решается поставленная нами задача, а именно уменьшение затрат на расходные материалы.
Изучив компании РФ, которые занимаются изготовлением устройств, был сделан вывод о том, что ни одна из компаний не изготавливают устройства.
В результате реализации нашего проекта, появляется возможность экспериментировать с различными материалами, считающимися «экзотичными» в мире 3D печати, но реально зачастую валяющиеся прямо под ногами.
Рис.6. Устройство в сборе для изготовления пластиковой нити для печати на 3D принтере (FDM)
С каждым днем 3D печать становится все более популярна среди обычных людей, они покупают себе принтеры и сталкиваются с проблемой того что пластик очень дорогой, но наш проект решает эту проблему и позволяет продавать пластик рядовым пользователям 3D принтеров, а так же и другим учебным заведениям в разы дешевле, чем производители филамента. Поэтому у проекта большие перспективы развития.
Литература:
- Сидоренко М. В. Профессии и компетенции будущего: практика и перспективы / М. В. Сидоренко // Вестник профессионального образования. — Хабаровск, 2019. — № 1. — С. 56–62.
- Обзор оборудования: металлические 3D принтеры HBD // Аддитивные технологии. — Москва, 2019. — № 2. — С. 32–35.
- Зленко М. А. Аддитивные технологии в машиностроении / М. В. Нагайцев М. В., В. М. Довбыш // пособие для инженеров. — М. ГНЦРФ ФГУП «НИМИ»: 2015. — 2020 с.