Рассматривается способ производства цельнометаллической просечно-вытяжной сетки из полосового металла методом опрессовки заготовки в специально разработанной просечной клети. Приведена методика расчета геометрии дисковых ножей для ее производства.
Ключевые слова: просечная клеть, цельнометаллическая просечно-вытяжная сетка, дисковые ножницы, конфигурация ножей
Современное производство цельнометаллической просечно-вытяжной сетки происходит по схеме поперечного реза с одновременным формированием ячейки. Из кинематической схемы, представленной на (рис. 1) видно, что стан для производства ПВЛ по данной технологии очень сложен с точки зрения ремонтов и обслуживания, что в свою очередь влияет на конечную цену производимой продукции.
Рис. 1. Кинематическая схема машины для изготовления просечно-вытяжной сетки
Метод, предложенный в данной статье позволяет производить сетку с ячейками трех видов, квадратная, ромбическая и шестигранная. Особенностью предлагаемой технологии является применение просечной клети, состоящей из двух пакетов ножей расположенных друг над другом и приводимых через шестеренчатую клеть [1]. Просечка заготовки, представляющей собой полосовой тонколистовой металл, производиться продольно относительно направления ее движения. Такой подход обеспечивает возможность, при условии дальнейшей разработки полноценной производственной линии и ввода ее в эксплуатацию, получить практически непрерывное производство просечного листа. На (рис. 2) представлен эскиз просечной клети.
Рис. 2. Эскиз просечной клети
Так как просечная клеть, по своей сути представляет многодисковые ножницы, применяемые для разделения полосового материала на более узкие полосы [2], то для изготовления сетки по данной технологии необходимо применять ножи определенной конфигурации. Ниже рассмотрена методика расчета и определения конфигурации ножей, для производства цельнометаллической просечно-вытяжной сетки с различной ячейкой.
Определение размеров иконфигурации ножей для шестигранной ячейки.
Все приведенные далее выкладки справедливы для расчета геометрии ножей для производства сетки с шестигранной ячейкой (рис. 3)
Рис. 3. Схема ножа для производства сетки с шестигранной ячейкой
Определение диаметра ножей для производства сетки с шестигранной ячейкой производиться по формуле:
(1)
(2)
где – диаметр ножа,
– длина окружности ножа,
– длина реза,
– количество режущих кромок.
Расчет углов и
проводиться по следующим формулам:
(3)
(4)
где

Радиус просвета для унификации производства выбран равным 6мм.
Определение размеров ножей для ромбической ячейкой.
Все приведенные далее выкладки справедливы для расчета геометрии ножей для производства сетки с ромбической ячейкой (рис. 4)
Рис. 4. Схема ножа для производства сетки с ромбической ячейкой
Определение диаметра ножей для производства сетки с шестигранной ячейкой производиться по формуле:
(5)
(6)
где – диаметр ножа,
– длина окружности ножа,
– длина реза,
– ширина стержня сетки,
– количество режущих кромок.
Расчет угла проводиться по формуле:

где – количество режущих кромок.
Радиус просвета для производства ножей под ромбическую ячейку соответствует
– ширине стержня сетки.
Определение размеров ножей для квадратной ячейкой.
Все приведенные далее выкладки справедливы для расчета геометрии ножей для производства сетки с квадратной ячейкой (рис. 5)
Рис. 5. Схема ножа для производства сетки с квадратной ячейкой
Определение диаметра ножей для производства сетки с квадратной ячейкой производиться по формуле:
(8)
(9)
где — диаметр ножа,
— длина окружности ножа,
— длина реза,
– количество режущих кромок.
Расчет углов


(10)
(11)
где – количество режущих кромок.
Радиус просвета для унификации производства выбран равным 6 мм.
Расчет углов заточки ножей.
Угол заточки ножей выбраны из расчета толщины ножа (т. е. ширины получаемого стержня, которая в свою очередь определена из условия увеличения сортамента производимой сетки), условия максимальной прочности режущей кромки (чем тупее угол заточки тем выше прочностные показатели ножа, что влияет на производительность станка) и толщины листа заготовки [3].
Все следующие проведенные расчеты приведены для определения угла заточки ножей (рис. 6)
Рис. 6. Схема определения угла заточки ножа
Соответствие толщины полосы заготовки и толщины дисковых ножей рассчитываются по формулам:
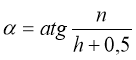
где – угол заточки дискового ножа,
– толщина ножа,
– толщина заготовки.
Размер 0,5 добавляется из расчета перекрытия ножей при резке металла малой толщины (< 4 мм.) значение которого задается от 0 до 3 мм [4]. Но главным условием для выбора такого размера стало ограничение по минимальному углу заточки ножей. Результаты проведенных расчетов приведены в таблице 1.
Таблица 1
Соотношение толщины полосы заготовки итолщины дисковых ножей
Толщина заготовки |
Толщина ножа |
Угол заточки |
2 |
5 |
63,43; 67,38 |
1,5 |
4 |
63,43; 68,19; 71,56 |
1 |
3 |
63,43; 69,44; 73,31 |
0,5 |
2 |
63,43; 71,57; 75,96 |
Литература:
- Анурьев В. И. Справочник конструктора-машиностроителя. В трех томах. Машиностроение, 2001, 913 с.
- Королев А. А. Конструкция и расчет машин и механизмов прокатных станов. Металлургия, 1985, 375 с.
- Малов А. Н. Технология холодной штамповки. Машиностроение, 1969, 568 с.
- Королев А. А. Механическое оборудование прокатных цехов. Металлургия, 1965, 512 с.