Предложен критерий упругопластического разрушения стальных труб большого диаметра при дефекте «раскатанный пригар с риской». Результаты исследования могут быть использованы при диагностике причин разрушения стальных труб большого диаметра магистральных газонефтепроводов.
Ключевые слова: стальные сварные трубы большого диаметра, критическое давление разрыва трубы, магистральный газонефтепровод, модель упругопластической сплошной среды.
Дефекты стальных труб газонефтепроводов. Современные магистральные трубопроводы состоят из огромного числа сваренных между собой стальных толстостенных труб большого диаметра. В трубопроводах присутствуют различные дефекты стенок стальных труб: расслоение металла, вмятины, коррозионные каверны, трещины, раскатные пригары, риски и т. д., которые существенно сокращают срок службы трубопроводных систем [15].
Для повышения безопасности и снижения металлоемкости магистральных трубопроводов применяют стальные толстостенные трубы большого диаметра с повышенной прочностью металла. В отечественных магистральных газонефтетрубопроводах используются стальные толстостенные сварные трубы большого диаметра 1020 мм, 1220 мм и 1420 мм из сталей класса прочностей К38−К65 и Х42−Х80, с толщиной стенки до 52 мм, длинной до 18 м и рабочим давлением до 22,15 МПа, изготовленные с помощью технологии JСОE фирмы SMS Meer [6−39]. Трубы изготовляют из широких толстостенных стальных листов, которые перед формовкой труб правят на многороликовых листоправильных машинах [4051].
Особую опасность представляют случаи, когда имеют место одновременно два источника разрушения, вызывающие концентрацию напряжений в стенках стальных труб газонефтепроводов. В данной работе рассматривается двойной источник разрушения стальных толстостенных труб большого диаметра на примере совместного действия дефекта раскатанный пригар и дефекта риска.
Дефект раскатанный пригар изучался в работах [31, 32, 52, 53], дефект риска в [31, 32, 54, 55], дефект несплавления сварного продольного шва в [31, 32, 5659], дефект образования гофра продольной кромки стального листа в работах [31, 32, 6, 10, 25, 38], дефект точка перегиба при изгибе стального листа на трубоформовочном прессе − в [31, 32, 19, 29, 36]. При достижении критических размеров эти дефекты часто приводят к разрушению трубопроводов [14, 60].
Пример разрушения трубы межпромыслового газопровода с образованием сквозного дефекта. В декабре 2010 г. произошла разгерметизация стальной трубы большого диаметра межпромыслового газопровода «УППГ Муравленковского нефтегазового месторожденияКомсомольский ГП» (Тюменская область) с образованием сквозного дефекта (рис. 1). Рабочее давление в момент инцидента − 4,4 МПа (59 % от проектного давления 7,5 МПа). Прочностные и геометрические характеристики трубы − класс прочности К60, диаметр 720 мм, толщина стенки 11 мм, длина 11,59 м, масса 2,251 т, внешнее трехслойное изоляционное покрытие. Стальной лист для трубы был изготовлен с помощью технологии контролируемой прокатки [31, 32].
Рис. 1. Сквозной дефект разгерметизированной стальной трубы
Дефект раскатанный пригар с риской представляет собой локальное утонение стенки трубы размером 110x50 мм. При разгерметизации трубопровода произошло выпадение пригара с образованием сквозного отверстия размером 20x25 мм. Выпавший пригар обнаружен не был.
Результаты механических испытаний металла. Механические характеристики металла трубы приведены в таблице 1.
Таблица 1
Результаты механических испытаний образцов металла трубы
Место отбора образцов |
Предел прочности σв, Н/мм2 |
Предел текучести σт, Н/мм2 |
Относительное удлинение 5, % |
Ударная вязкость KCV при 20°C, Дж/см2 |
Ударная вязкость KCU при 60°C, Дж/см2 |
Основной металл |
686 |
617 |
20,0 |
163 |
196 |
686 |
617 |
20,0 |
153 |
183 |
|
684 |
614 |
21,8 |
152 |
188 |
|
Среднее 685,3 |
Среднее 616 |
Среднее 21,3 |
Среднее 156 |
Среднее 189 |
|
ТУ 1381–012–05757848–2005 |
Не менее 590 |
Не менее 480 |
Не менее 20 |
Не менее 39,2 |
Не менее 49,0 |
Из таблицы 1 следует, что по результатам механических испытаний основной металл трубы (металл вне дефекта и сварных соединений) соответствует требованиям ТУ 1381–012–05757848–2005 для стали класса прочности К60.
Рис. 2. Микроструктура основного металла трубы в 300 мм от места дефекта
Результаты металлографических исследований структуры металла. Результаты металлографических исследований металла стенки стальной трубы показаны на рис. 24. При определении микроструктуры металла выполнено травление шлифов четырехпроцентным раствором азотной кислоты в этиловом спирте. Первый образец металла вырезан на расстоянии 300 мм от места дефекта. Его структура была принята за исходную. Основной металл трубы по химическому составу и механическим свойствам соответствует требованиям ТУ 1381–012–05757848–2005 для стали класса прочности К60 (рис. 2).
Второй образец вырезан в месте дефекта раскатной пригар в плоскости, поперечной направлению проката листа. Полосчатость перлита по сечению образца неоднородна. На образце у поверхности, примыкающей к дефекту, наблюдается локальное искажение однонаправленности перлитной полосчатости (рис. 3). Данные искажения структуры показывают, что дефект был сформирован при горячей деформации в процессе прокатки листа. Отсутствие в структуре выраженного огибания дефектного участка по всей его протяженности, а так же форма дефектного участка показывают, что дефект не был вдавлен в лист, как инородное тело отличной от листа плотности и температуры, а являлся частью литой заготовки, то есть деформировался при прокатке вместе с листом как единое целое (рис. 1).
Рис. 3. Микроструктура металла в области раскатанного пригара
Третий образец металла вырезан в месте дефекта в плоскости, параллельной направлению проката листа. На третьем образце также наблюдается локальное искажение направленности перлитной полосчатости (рис. 4).
Микроструктура основного металла трубы на всех шлифах феррито-перлитная с баллом зерна 910 по ГОСТ 5639–82. Полосчатость соответствует баллу № 2 ряда Б по ГОСТ 5640–68 (рис. 24).
В результате исследования трех темплетов, вырезанных из разгерметизированной трубы, установлено, что основной металл трубы по химическому составу также соответствует требованиям ТУ 1381–012–05757848–2005 для стали класса прочности К60.
Рис. 4. Микроструктура металла в области риски
Причины образования дефекта. Размеры и вид сквозного отверстия разорванной трубы на ее внешней и внутренней поверхностях свидетельствуют в пользу того, что причиной дефекта раскатанный пригар с риской вероятно послужило падение шестигранной гайки типа М12 (ГОСТ 5915–70, ширина 19 мм, диагональ 21,94 мм, толщина 10 мм) или М14 (ГОСТ 5927–70, ширина 21 мм, диагональ 24,25 мм, толщина 11 мм) на поверхность раскаленного листа при прокатке. До момента вдавливания в горячий лист температура гайки была значительно ниже температуры листа. Валки при прокатке не сразу захватили гайку и от нее на поверхности листа образовалась риска с постепенно увеличивающимися глубиной и поперечным размером. Максимальный поперечный размер риски равен размеру гайки в момент ее вдавливания в лист. Вдавливание гайки в горячий лист было моментальным и привело к локальному повышению температуры металла внутри стенки листа до температуры, сравнимой с температурой плавления металла, и выбросу части полужидкого металла наружу. Это вызвало значительное увеличение размеров дефекта стенки листа в направлении его верхней поверхности. Так как температура «упругой» гайки была еще существенно ниже температуры раскаленного «пластического» листа, гайка легко вдавилась в лист практически на полную толщину листа. После вдавливания гайки в горячий лист, ее температура резко увеличилась и приблизилась к температуре листа. При прокатке гайки с листом как единого целого через несколько валков толщина гайки уменьшилась, а поперечные размеры гайки увеличились и приобрели овальные очертания.
Рис. 5. Дефект раскатанный пригар на внешней поверхности трубы
Критерий упругопластического разрыва трубы при дефекте «раскатанный пригар с риской». Раскатанный пригар − дефект поверхности стального листа в виде тёмного пятна неправильной формы, образовавшийся от раската куска металла, приварившегося к слябу из-за нарушения технологии разливки или упавшего на поверхность листа при горячей прокатке [5]. При выгорании или выпадении раскатанного пригара на поверхности листа остаются углубления с разрывами по краям.
Риска (царапина) − дефект поверхности трубы в виде канавки без выступа кромок с закругленным или плоским дном, образовавшийся от царапания поверхности металла листа или трубы прокатной арматурой без изменения структуры и неметаллических включений [5].
Пусть p − внутреннее давление трубы; h и D − толщина стенки и внешний диаметр трубы (h << D), σв − предел прочности материала трубы; a, b и Δ − продольный и поперечный размеры раскатного пригара и глубина пригара в стенке трубы (Δ < h); a1 и Δ1 − максимальные ширина и глубина риски от раскатного пригара (Δ1 ≤ Δ), φ1 и φ2 − углы наклона «продольных осей» пригара и риски, соответственно, к окружности поперечного сечения и образующей трубы (рис. 5).
Под действием внутреннего давления металл стенки трубы в зоне дефекта раскатанный пригар с риской испытывает сложное сопротивление: окружное растяжение, радиальное сжатие и концентрацию напряжений. По теории прочности внешняя стенка трубы разрушается, когда максимальные касательные напряжения достигают половины предела прочности σв. Разрушение стенки трубы при дефекте раскатанный пригар происходит при достижении в трубе критического давления (критерий Шинкина разрушения трубы при дефекте раскатанный пригар с риской):
где μ = const ≥ 1 − безразмерный коэффициент (определяется экспериментально); коэффициент учитывает концентрацию напряжений в стенке трубы от раскатного пригара с учетом глубины риски, а коэффициент
− от ширины и глубины риски.
Подставляя в вышеприведенный критерий параметры вышеуказанной разгерметизированной трубы, получаем при = 1 значение pshкритич = 4,547 МПа, которое отличается от реального давления разрыва трубы 4,4 МПа всего на 3,34 %.
Пластическая деформация стенки трубы начинается при давлении
Результаты численных расчетов. Расчет критических давлений при μ = 1, D = 720 мм, h = 11 мм, σв = 684 МПа, σт = 614 МПа, Δ1 = 3 мм, a = 20 мм, b = 25 мм, a1 = 20 мм, φ1 = 10,4о, φ2 = 34,3о в зависимости от глубины раскатного пригара Δ (h > Δ ≥ Δ1) в стенке трубы приведен в таблице 2.
Таблица 2
Результаты расчета критических давлений труб
Δ, мм |
3 |
4 |
5 |
6 |
7 |
8 |
9 |
10 |
pshкритич, МПа |
9,915 |
8,484 |
7,414 |
6,584 |
5,921 |
5,379 |
4,928 |
4,547 |
pshпластич, МПа |
8,900 |
7,616 |
6,655 |
5,910 |
5,315 |
4,829 |
4,424 |
4,082 |
На рис. 6 показана зависимость критического напряжения pshкритич от толщины стенки трубы h (11 мм h 40 мм) при μ = 1, σв = 684 МПа, D = 720 мм, = 10 мм, Δ1 = 3 мм, a = 20 мм, b = 25 мм, a1 = 20 мм, φ1 = 10,4о, φ2 = 34,3о.
Рис. 6. Зависимость критического напряжения pshкритич от толщины стенки трубы h
На рис. 7 показана зависимость критического напряжения pshкритич от глубины раскатанного пригара (3 мм 11 мм) при μ = 1, σв = 684 МПа, D = 720 мм, h = 11 мм, Δ1 = 3 мм, a = 20 мм, b = 25 мм, a1 = 20 мм, φ1 = 10,4о, φ2 = 34,3о.
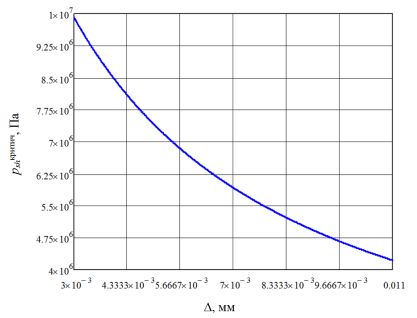
Рис. 7. Зависимость критического напряжения pshкритич от глубины раскатанного пригара
На рис. 8 показана зависимость критического напряжения pshкритич от глубины риски 1 (3 мм 1 10 мм) при μ = 1, σв = 684 МПа, D = 720 мм, h = 11 мм, = 10 мм, a = 20 мм, b = 25 мм, a1 = 20 мм, φ1 = 10,4о, φ2 = 34,3о.
Рис. 8. Зависимость критического напряжения pshкритич от глубины риски 1
На рис. 9 показана зависимость критического напряжения pshкритич от отношения a/b (0 a/b 1) при μ = 1, σв = 684 МПа, D = 720 мм, h = 11 мм, = 10 мм, Δ1 = 3 мм, a1 = 20 мм, φ1 = 10,4о, φ2 = 34,3о.
Рис. 9. Зависимость критического напряжения pshкритич от отношения a/b
На рис. 10 показана зависимость критического напряжения pshкритич от ширины риски a1 (0 мм a1 25 мм) при μ = 1, σв = 684 МПа, D = 720 мм, h = 11 мм, = 10 мм, Δ1 = 3 мм, a = 20 мм, b = 25 мм, φ1 = 10,4о, φ2 = 34,3о.
Рис. 10. Зависимость критического напряжения pshкритич от ширины риски a1
На рис. 11 показана зависимость критического напряжения pshкритич от угла раскатанного пригара φ2 (0 φ2 /2) при μ = 1, σв = 684 МПа, D = 720 мм, h = 11 мм, = 10 мм, Δ1 = 3 мм, a = 20 мм, b = 25 мм, a1 = 20 мм, φ1 = 10,4о.
Рис. 11. Зависимость критического напряжения pshкритич от угла раскатанного пригара φ2
На рис. 12 показана зависимость критического напряжения pshкритич от угла риски 1 (0 1 /2) при μ = 1, σв = 684 МПа, D = 720 мм, h = 11 мм, = 10 мм, Δ1 = 3 мм, a = 20 мм, b = 25 мм, a1 = 20 мм, φ2 = 34,3о.
Рис. 12. Зависимость критического напряжения pshкритич от угла риски 1
На рис. 13 показана зависимость критического напряжения pshкритич от глубины (3 мм 10 мм) и угла φ2 (0 φ2 /2) раскатанного пригара при μ = 1, σв = 684 МПа, D = 720 мм, h = 11 мм, Δ1 = 3 мм, a = 20 мм, b = 25 мм, a1 = 20 мм, φ1 = 10,4о.
Рис. 13. Зависимость критического напряжения pshкритич от глубины и угла φ2 раскатанного пригара
На рис. 14 показана зависимость критического напряжения pshкритич от глубины риски 1 (0 мм 1 10 мм) и угла φ2 (0 φ2 /2) раскатанного пригара при μ = 1, σв = 684 МПа, D = 720 мм, h = 11 мм, = 10 мм, a = 20 мм, b = 25 мм, a1 = 20 мм, φ1 = 10,4о.
Рис. 14. Зависимость критического напряжения pshкритич от глубины риски 1 и угла φ2 раскатанного пригара
На рис. 15 показана зависимость критического напряжения pshкритич от ширины риски a1 (0 мм a1 25 мм) и угла φ2 (0 φ2 /2) раскатанного пригара при μ = 1, σв = 684 МПа, D = 720 мм, h = 11 мм, = 10 мм, Δ1 = 3 мм, a = 20 мм, b = 25 мм, φ1 = 10,4о.
Рис. 15. Зависимость критического напряжения pshкритич от ширины риски a1 и угла φ2 раскатанного пригара
Литература:
- Мазур И. И., Иванцов О. М. Безопасность трубопроводных систем. - М: ИЦ «ЕЛИМА», 2004. - 1104 с.
- Коршак А. А., Нечваль А. М. Проектирование и эксплуатация газонефтепроводов. - СПб.: Недра, 2008. - 488 с.
- Демченко В. Г., Демченко Г. В. Магистральные трубопроводы. Надежность. Условия работы и разрушений. - М.: Недра, 2007. - 304 с.
- Тетельмин В. В., Язев В. А. Магистральные нефтегазопроводы. - Долгопрудный: Изд. Дом «Интеллект», 2010. - 352 с.
- ГОСТ 21014–88. Прокат черных металлов. Термины и определения дефектов поверхности. - М.: ГК СССР по стандартам, 1988. - 62 с.
- Шинкин В. Н. Гофр продольной кромки листа при его формовке на кромкогибочном прессе // Машиностроение и безопасность жизнедеятельности. 2009. Вып. 6. С. 171−174.
- Шинкин В. Н., Уандыкова С. К. Гибка стальной листовой заготовки на кромкогибочном прессе при производстве труб большого диаметра // Известия Кыргызского государственного технического университета им. И. Раззакова. 2009. № 16. С. 110−112.
- Шинкин В. Н., Коликов А. П. Моделирование процесса формовки заготовки для труб большого диаметра // Сталь. 2011. № 1. С. 54−58.
- Шинкин В. Н., Коликов А. П. Моделирование процесса пластического формоизменения листовой заготовки для производства труб большого диаметра // Обработка металлов давлением, 2011. № 3(28). С. 7-11.
- Шинкин В. Н., Коликов А. П. Формовка листовой заготовки в кромкогибочном прессе и условие возникновение гофра при производстве труб магистральных трубопроводов // Производство проката. 2011. № 4. С. 14−22.
- Шинкин В. Н. Математическое моделирование процессов производства труб большого диаметра для магистральных трубопроводов // Вестник Саратовского государственного технического университета. 2011. № 4 (62). Вып. 4. С. 69−74.
- Шинкин В. Н., Коликов А. П. Упругопластическое формоизменение металла на кромкогибочном прессе при формовке труб большого диаметра // Сталь. 2011. № 6. С. 53-56.
- Шинкин В. Н., Коликов А. П. Модель пластического формоизменения кромок листовой заготовки при производстве труб большого диаметра для магистральных трубопроводов // Известия вузов. Черная металлургия. 2011. № 9. С. 45-49.
- Шинкин В. Н., Коликов А. П. Моделирование процессов экспандирования и гидроиспытания труб большого диаметра для магистральных трубопроводов // Производство проката. 2011. № 10. С. 12−19.
- Шинкин В. Н., Коликов А. П., Барыков А. М. Технологические расчеты процессов производства труб большого диаметра по технологии SMS Meer // Металлург. 2011. № 11. С. 77−81.
- Shinkin V. N., Kolikov A. P. Simulation of the shaping of blanks for large-diameter pipe // Steel in Translation. 2011. Vol. 41. No. 1. P. 61-66.
- Shinkin V. N., Kolikov A. P. Elastoplastic shaping of metal in an edge-ending press in the manufacture of large-diameter pipe // Steel in Translation. 2011. Vol. 41. No. 6. P. 528-531.
- Шинкин В. Н., Коликов А. П., Мокроусов В. И. Расчет максимальных напряжений в стенке трубы при экспандировании с учетом остаточных напряжений заготовки после трубоформовочного пресса SMS Meer // Производство проката. 2012. № 7. С. 25−29.
- Шинкин В. Н. Критерий перегиба в обратную сторону свободной части листовой заготовки на трубоформовочном прессе SMS Meer при производстве труб большого диаметра // Производство проката. 2012. № 9. С. 21−26.
- Shinkin V. N., Kolikov A. P. Engineering calculations for processes involved in the production of large-diameter pipes by the SMS Meer technology // Metallurgist. 2012. Vol. 55. Nos. 11-12. P. 833-840.
- Шинкин В. Н., Барыков А. М. Расчет формы трубной заготовки при гибке на кромкогибочном и трубоформовочном прессах фирмы SMSMeer при производстве труб большого диаметра по схеме JCOE // Производство проката. 2014. № 12. С. 13−20.
- Шинкин В. Н., Барыков А. М. Гибка стального листа на трубоформовочном прессе при производстве труб большого диаметра // Сталь. 2015. № 4. С. 38−42.
- Шинкин В. Н. Производство труб большого диаметра по схеме JCOE фирмы SMSMeer для магистральных трубопроводов // Актуальные проблемы гуманитарных и естественных наук. 2015. № 3-1. С. 64-67.
- Шинкин В. Н. Расчет технологических параметров кромкогибочного пресса фирмы SMSMeer // Актуальные проблемы гуманитарных и естественных наук. 2015. № 4-1. С. 114-119.
- Шинкин В. Н. Математический критерий возникновения гофра при формовке стальной листовой заготовки на кромкогибочном прессе SMSMeer // Актуальные проблемы гуманитарных и естественных наук. 2015. № 5-1. С. 96–99.
- Шинкин В. Н. Расчет усилий трубоформовочного пресса SMSMeer при изгибе плоской толстой стальной заготовки при производстве труб большого диаметра // Актуальные проблемы гуманитарных и естественных наук. 2015. № 6-1. С. 115–118.
- Шинкин В. Н. Оценка усилий трубоформовочного пресса SMSMeer при изгибе стальной цилиндрической заготовки // Актуальные проблемы гуманитарных и естественных наук. 2015. № 7-1. С. 74-78.
- Шинкин В. Н., Барыков А. М. Сила давления пуансона трубоформовочного пресса SMSMeer при изгибе частично изогнутой толстой стальной заготовки // Актуальные проблемы гуманитарных и естественных наук. 2015. № 8-1. С. 78-83.
- Шинкин В. Н., Барыков А. М. Математический критерий перегиба стальной заготовки на трубоформовочном прессе SMSMeer // Актуальные проблемы гуманитарных и естественных наук. 2015. № 9-1. С. 73-77.
- Шинкин В. Н. Влияние остаточных напряжений на прочность металла при экспандировании стальной заготовки // Актуальные проблемы гуманитарных и естественных наук. 2015. № 10-1.
- Шинкин В. Н. Сопротивление материалов для металлургов. - М: Изд. Дом МИСиС, 2013. - 655 с.
- Шинкин В. Н. Механика сплошных сред для металлургов. - М: Изд. Дом МИСиС, 2014. - 628 с.
- Шинкин В. Н. Сопротивление материалов. Простые и сложные виды деформаций в металлургии. - М: Изд. Дом МИСиС, 2008. - 307 с.
- Шинкин В. Н. Теоретическая механика для металлургов. - М: Изд. Дом МИСиС, 2012. - 679 с.
- Буланов Э. А., Шинкин В. Н. Механика. Вводный курс. - М.: БИНОМ. Лаборатория знаний, 2013. - 172 с.
- Шинкин В. Н. Дефект перегиба стальной заготовки на трубоформовочном прессе // Молодой ученый. 2015. № 17 (97). С. 318-323.
- Шинкин В. Н. Подгибка кромок стального листа по эвольвенте // Молодой ученый. 2015. № 18 (98). С. 231-237.
- Шинкин В. Н. Критерий образования гофра при формовке стального листа на кромкогибочном прессе SMSMeer // Молодой ученый. 2015. № 19 (99). С. 238-243.
- Шинкин В. Н. Остаточные напряжения при экспандировании стальной трубы // Молодой ученый. 2015. № 20 (100). С. 88-93.
- Шинкин В. Н., Федотов О. В. Расчет технологических параметров правки стальной горячекатаной рулонной полосы на пятироликовой машине линии поперечной резки фирмы Fagor Arrasate // Производство проката. 2013. № 9. С. 43-48.
- Шинкин В. Н., Барыков А. М. Расчет технологических параметров холодной правки стального листа на девятироликовой машине SMS Siemag металлургического комплекса стан 5000 // Производство проката. 2014. № 5. С. 7-15.
- Шинкин В. Н. Расчет технологических параметров правки стального листа на одиннадцатироликовой листоправильной машине линии поперечной резки фирмы Fagor Arrasate // Производство проката. 2014. № 8. С. 26-34.
- Шинкин В. Н., Борисевич В. Г., Федотов О. В. Холодная правка стального листа в четырехроликовой листоправильной машине // В сборнике: Глобализация науки: проблемы и перспективы. Том 2. - Уфа: Башкирский государственный университет, 2014. - С. 119-121.
- Шинкин В. Н. Математическая модель правки тонкого стального листа на пятнадцатироликовой листоправильной машине линии поперечной резки фирмы Fagor Arrasate // Производство проката. 2015. № 1. С. 42−48.
- Шинкин В. Н. Математическая модель правки стальной полосы на пятироликовой листоправильной машине фирмы FagorArrasate // Молодой ученый. 2015. № 8 (88). С. 344-349.
- Шинкин В. Н. Правка толстой стальной полосы на одиннадцатироликовой листоправильной машине линии поперечной резки фирмы FagorArrasate // Молодой ученый. 2015. № 9 (89). С. 359-365.
- Шинкин В. Н. Расчет технологических параметров правки тонкой стальной полосы на пятнадцатироликовой листоправильной машине фирмы FagorArrasate // Молодой ученый. 2015. № 10 (90). С. 361-366.
- Шинкин В. Н. Холодная правка толстого стального листа на девятироликовой машине фирмы SMSSiemag на металлургическом комплексе стан 5000 // Молодой ученый. 2015. № 11 (91). С. 467–472.
- Шинкин В. Н. Четырехроликовый режим холодной правки толстого стального листа на пятироликовой листоправильной машине фирмы FagorArrasate // Молодой ученый. 2015. № 12 (92). С. 356–361.
- Шинкин В. Н. Упругопластическая деформация металлического листа на трехвалковых вальцах // Молодой ученый. 2015. № 13 (93). С. 225–229.
- Шинкин В. Н. Шестироликовый режим предварительной правки стальной полосы на листоправильной машине фирмы FagorArrasate // Молодой ученый. 2015. № 14 (94). С. 205–211.
- Шинкин В. Н. Критерий разрыва трубы при внутреннем давлении и дефекте раскатной пригар на поверхности трубы // Высокие технологии, исследования, промышленность. − СПб.: Изд-во Политехн. Ун-та, 2011. Т.3. Часть 2. С. 289-290.
- Шинкин В. Н. Критерий разрушения труб при дефекте раскатной пригар // Молодой ученый. 2015. № 16 (96). С. 261-265.
- Мокроусов В. И. К вопросу о разрушении стальных труб большого диаметра при дефекте риска на внешней поверхности трубы // Молодой ученый. 2015. № 18 (98). С. 168-172.
- Мокроусов В. И. Влияние на прочность стальных толстостенных труб дефекта риска на внутренней поверхности // Молодой ученый. 2015. № 19 (99). С. 148-153.
- Шинкин В. Н., Барыков А. М., Коликов А. П., Мокроусов В. И. Критерий разрушения труб большого диаметра при несплавлении сварного соединения и внутреннем давлении // Производство проката. 2012. № 2. С. 14−16.
- Шинкин В. Н. Определение критических давлений магистральных газонефтепроводов при частичном несплавлении продольного сварного шва стальных толстостенных труб // Молодой ученый. 2015. № 15 (95). С. 222-227.
- Шинкин В. Н. Оценка критических давлений при разрушении стальных труб магистральных газонефтепроводов при несплавлении сварного соединения // Современная наука: актуальные проблемы теории и практики. Серия: Естественные и технические науки. 2015. № 5-6. С. 7-11.
- Мокроусов В. И. Прочность стальных труб при дефекте внешней фаски продольного сварного шва // Молодой ученый. 2015. № 20 (100). С. 44-49.
- Ланчаков Г. А., Зорин Е. Е., Пашков Ю. И., Степаненко А. И. Работоспособность трубопроводов. Часть 2. Сопротивляемость разрушению. - М.: Недра, 2001. - 350 с.